Northern Liberties Passive
Rowhouse
Energy Efficiency Strategies and Data
Design and Performance
Developing a deep understanding of each project’s physical, historic, and social context is a priority as we begin each project. As the creative process unfolds, we strategize about how first tier performance strategies can inform and strengthen the design.
The project team quickly identified that the project was to be ambitious in terms of energy use. Iterative massing, program, and fenestration studies allowed us to understand and refine solar exposure and envelope requirements.
Once Schematic Design was complete, the project team, including the general contractor and consulting engineers, collaboratively worked to develop the home’s structural, heating/cooling/ventilation, plumbing, and electrical systems. We refined them to maximize efficiency, and analyzed the design against other important parameters such as the quality of the interior space, and the project cost.
A Brief Summary of the Building Systems
-
The foundation of the building is poured in place concrete with 3” of continuous exterior EPS insulation on the walls and slab, as well as 3” of continuous EPS and R-10 cavity insulation on the interior of the foundation wall. Aside from a steel moment frame at the garage door, the super structure is conventional wood framing. The stair from levels 1-2, is a custom designed powder coated steel frame with white oak treads.
-
An important aspect of passive house design is continuous ventilation. The project team chose to integrate the HVAC system and ventilation system using the Minotair Pentacare Heat Recovery Ventilator, a Combination Dehumidifier, Air Source heat pump, HEPA MERV 15 Air Filter and Heat Recovery Ventilator. Two Minotair units serve the house with one located in the basement and one in a second floor closet. They are hung from the ceiling and are extremely quiet.
-
There is a 200 amp electrical service that is tied to a Lumin smart electric panel and 3.24 kW DC photovoltaic array (located on the roof) with battery storage and off grid capability. The PV array is made by LG, with Enphase Micro inverters, and was installed by Solar States. There is also an electric car charger in the garage.
-
The home has a domestic water supply and drainage to the city services located in Orkney street. There is a recirculating pump which ensures immediate hot water to the primary bathroom (and thus saves water - no wait!)
-
The building is fully sprinklered with an NFPA 13R system according to Philadelphia building code.
Into the Details
The Building Envelope:
Typical Wall Assembly:
R38 (includes 4” continuous exterior insulation)
Roof Assembly:
Min R60 (includes minimum 5” continuous exterior insulation)
Foundation Walls:
R34 (inlcludes 3” continuous exterior insulation)
Floor Slab:
R12 (3” continuous insulation below slab)
Floor (Above Garage):
R51 (includes 1.5” continuous insulation)
Windows/Exterior Doors:
Alpen ZR-9 Series: U Value 0.12-0.15, SHGC: 0.23-0.3
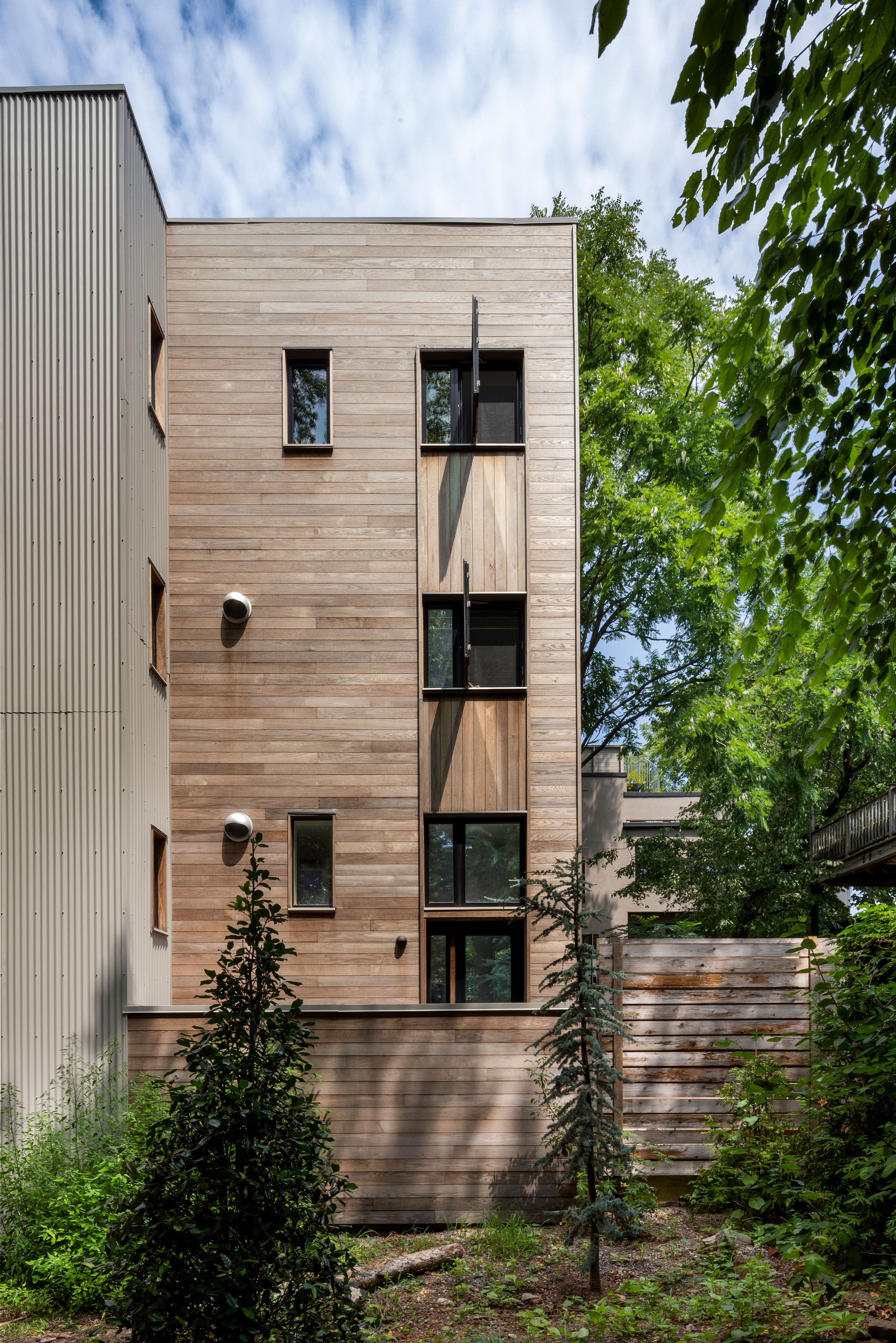
Local Materials
The exterior cladding is thermally modified red oak, sourced from Americana Hardwoods, based in Pennsylvania.
PHIUS Certification
Air Sealing at 50pa:
Blower door test result: 0.05 CFM/sf
(=0.34 ACH, code requires 3 ACH)
Heating Demand:
Target: 5.7 kBTU/sf/yr
Achieved: 5.61 kBTU/sf/yr
Cooling Demand:
Target: 9.8 kBTU/sf/yr
Achieved: 6.59 kBTU/sf/yr
Heating Load:
Target: 5.5 Btu/sf/hr
Achieved: 4.68 Btu/sf/hr
Cooling Load:
Target: 4 Btu/sf/hr
Achieved: 3.27 Btu/sf/hr
Home Energy:
5.24 kwh/yr
Lessons Learned
The implementation of high performance strategies should be a goal for every building project: not only do they reduce energy use, but they make buildings healthier, more comfortable, and more resilient. LTD has the expertise to evaluate the complexity and cost of these goals, and our team is able to work with clients to achieve them as is possible on a project to project basis.